

Infocareer® has been helping small and medium scale Manufacturing organizations in transitioning to a new business environment by improving their Supply-Chain systems to achieve efficiency using Lean Manufacturing processes. The goal is to provide the customer with a defect free product or service when it is needed and in the quantity it is needed.
We help organizations implement Lean tools and techniques in the following areas of production:
- Improve Quality
- Eliminate Waste
- Reduce Cycle Time
- Reduce Total Cost
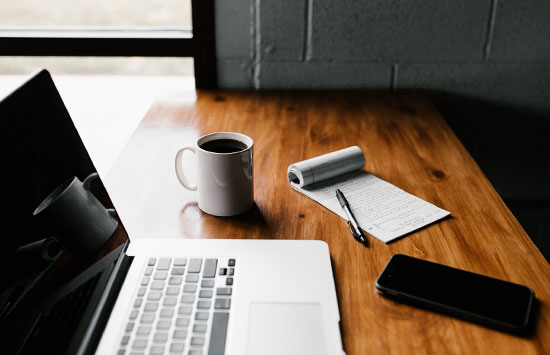
Some of the Lean practices implemented by Infocareer® in manufacturing SME’s include:
- 5S System
- Standard Operating Procedures (SOP)
- Kaizen Blitz or Rapid Process Improvement
- Value Stream Mapping
- Total Productive Maintenance (TPM)
- Single Minute Exchange of Dies / Quick Changeover
- Visual Controls
- Just in Time
- Cellular layout
- Poke Yoke or Mistake Proofing
- Kanban Systems
The objective is to enhance the manufacturing competitiveness of SME’s through the application of various Lean Manufacturing (LM) techniques by:
- Reducing waste
- Increasing productivity
- Introducing innovative practices for improving overall competitiveness;
- Imbibing a culture of continuous improvement.
The general approach involves engagement of our Lean Manufacturing Consultants (LMC) to work with the SMEs to reduce their manufacturing costs through proper personnel management, better space utilization, scientific inventory management, improved process flows, and reduced engineering time and so on with the application of LM techniques to reduce “waste” in manufacturing.
The interventions lead to increase in competitiveness of the manufacturing units i.e. They can manufacture better quality products with less cost by improvement in process flow, standardization of process, reduction in waste, processing time, etc. The extent of tangible benefits depends upon the scope of improvement, benchmarking, involvement of the entrepreneurs/units. All these aspects are studied and included in the Diagnostic Study Report which is prepared by the LM Consultant at the start of the interventions at the field level.
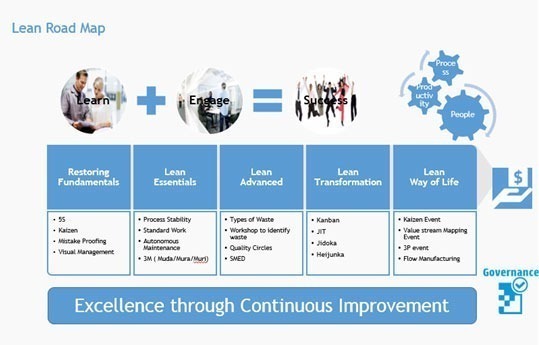